News & Events
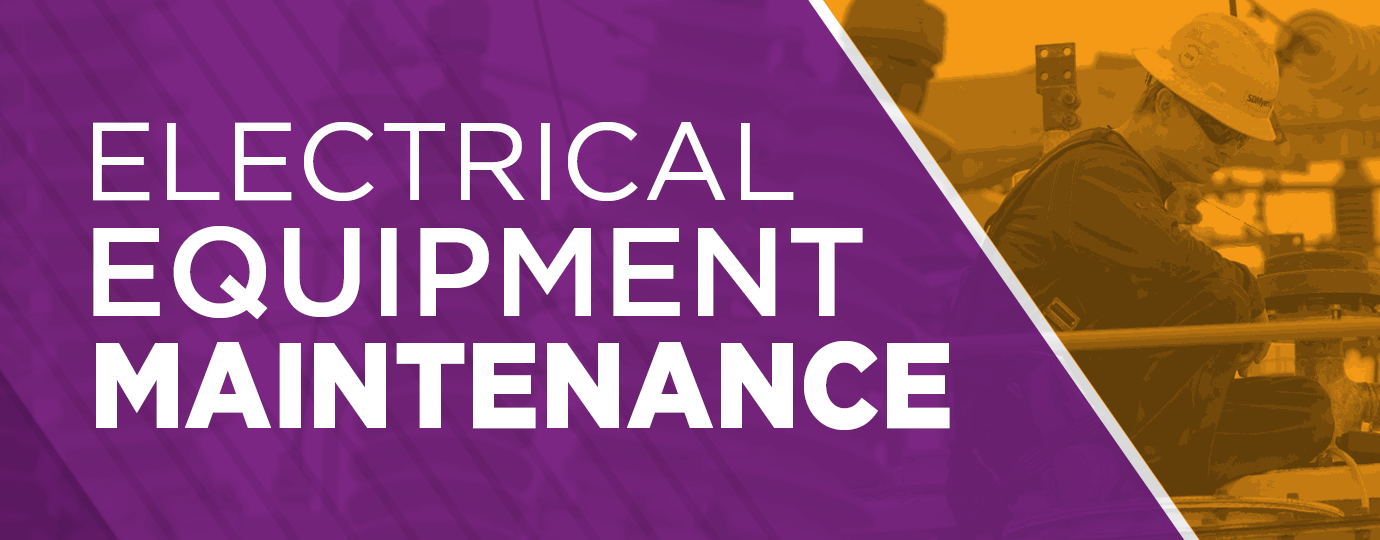
Which Approach to Electrical Equipment Maintenance is Best?
When it comes to maintaining electrical equipment, it's important to consider a few strategies to ensure optimal performance, reliability, longevity, and low costs. There are several popular approaches to electrical equipment maintenance, and over the years, SDMyers has seen it all. Ultimately, we aim to partner with organizations in implementing transformer maintenance that helps minimize downtime and prevent costly breakdowns.
Popular Maintenance Strategies:
- Corrective Maintenance
- Preventative Maintenance
- Risk-Based Maintenance
- Condition-Based Maintenance
Let’s briefly explore each of these maintenance strategies.
Corrective Maintenance
Corrective maintenance refers to repairing or fixing equipment or machinery when it has malfunctioned or failed. This type of maintenance is typically reactive and is performed after a problem has already occurred. Corrective maintenance is an essential aspect of equipment maintenance as it helps to restore equipment to its optimal operating condition and prevents further damage or breakdowns. Because it happens after a failure, downtime or interruptions to production could be costly—especially for mission-critical operations. For most organizations, unplanned outages due to a transformer failure could cost tens of thousands, if not millions, of dollars. Relying solely on corrective maintenance for your transformer isn’t the best approach. However, it is essential for businesses and organizations to have a plan in place for corrective maintenance to ensure that equipment downtime is minimized and operations can resume smoothly.
Preventative Maintenance
Preventative maintenance is a proactive approach to equipment maintenance that involves regularly scheduled inspections, testing, and servicing to prevent equipment failure or malfunctions before they occur. This type of maintenance is designed to identify and address potential issues before they become significant problems—minimizing downtime and reducing repair costs. Types of activities in this category could include annual transformer oil testing or moisture reduction plans. Preventative maintenance is an important aspect of transformer maintenance and can help businesses and organizations to optimize their operations and extend the lifespan of their transformer.
Risk-Based Maintenance
Risk-based maintenance is a type of maintenance strategy that prioritizes maintenance tasks based on the level of risk they pose to a facility or equipment. By identifying potential risks and focusing on preventive maintenance activities, this approach can help mission-critical operations stay up and running while extending equipment life and improving safety. It involves analyzing and using data to make informed decisions about maintenance priorities. It's a proactive approach to transformer maintenance that can help organizations maximize their resources and minimize the impact of maintenance-related issues.
Condition-Based Maintenance
Condition-based maintenance (CBM) is a maintenance strategy that monitors the real-time condition of an asset to provide data and insight to make informed, cost-effective, and efficient maintenance decisions. Unlike preventive maintenance, which operates on routine calendar-based activities, condition-based maintenance seeks to prevent failures (and downtime!) by monitoring and analyzing irregularities, trending data, or indicators of decreased performance. The benefits of condition-based maintenance include increased reliability, lower long-term maintenance costs, lower risks of downtime, better prioritization of resources, and maximum asset life. For transformer owners, these benefits translate directly to the bottom line and a just as valuable peace of mind.
Which is the best maintenance strategy?
The best maintenance strategy will depend on various factors, including the type of electrical equipment, its age and condition, the criticality of the operations, and the needs of the organization.
It is vitally important to define a fleet of transformers by their criticality, risk, and history so it is possible to prioritize resources with which to perform maintenance. Developing a ranking and asset class (e.g., Non-critical, Auxiliary, System Critical, and Mission Critical) can help you evaluate and choose a combination of maintenance strategies that make sense for each asset.
For example, non-critical assets can use fewer maintenance resources with basic corrective maintenance after a failure occurs versus mission-critical assets, which should receive highly attentive condition-based maintenance activities.
By evaluating these factors and choosing a combination of these maintenance approaches, organizations can ensure their equipment remains reliable, efficient, and cost-effective over the long term.
Talk to a Transformer Specialist Today
More than a half-century of transformer maintenance experience is just a click or a call away. If transformer reliability is your responsibility, we’re ready to partner with you in keeping your operation running. Take control of your transformer reliability today.
May 30, 2023