News & Events
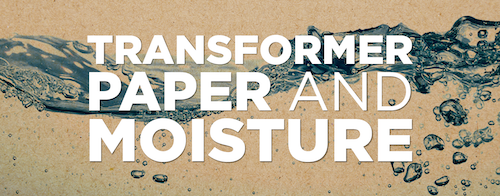
Your Transformer Paper & Moisture
Most transformer failures are the ones we can see coming—if we’re looking at the right things. Moisture content is one of those measurable factors every transformer owner should look at, and it is a tremendously valuable predictor of failure. After more than five decades of servicing transformers, we know all too well that the weakest link in the system is where moisture loves to hide—the paper insulation.
Moisture Levels in Paper
Transformer owners must consider the moisture content of the liquid insulation (the oil) as only a partial indicator of the amount of moisture in a transformer. The paper insulation has 100 times or more affinity for moisture compared to the oil. Moisture prefers paper over oil, which means the key to a dry transformer is keeping the paper dry.
On average, a 1,000-gallon transformer might have 1,170 lb. of solid insulation. Using 30 ppm and one of several industry algorithms that estimate the solid insulation dryness from an oil sample, the moisture by dry weight (M/DW) can be estimated at 2%. The total moisture in the insulation would then be 2% of 1,170 or 23.4 lb.
At this moisture level, there is 106 times (23.4 lb./0.22 lb.) more moisture in the paper than in the oil. Therefore, moisture must be removed from the oil and the solid insulation to ensure the transformer delivers its maximum reliable life. Dehydrating only the oil will result in a temporary fix. Within weeks of an oil-dehydration procedure, the moisture content will become unacceptable again as moisture trapped in the paper migrates into the oil. Dehydrating the oil doesn’t remove the moisture in the paper unless the moisture is within the top surface layer.
Damage to the Paper is Irreversible
Testing for moisture and keeping it at acceptable levels is vitally important for transformer owners because the condition of the paper insulation is the primary limiting factor to the life of a transformer. The unit is permanently weakened if the paper becomes compromised by moisture and oxidation. Once this damage occurs, it is irreversible—it can be slowed or stopped but not reversed.
Permanent damage from moisture and oxidation leads to premature loss of equipment life. Replacing a transformer is costly, which makes moisture reduction a priority. While the unit may not be at risk of immediate failure, gradual increases in the percent moisture by dry weight of the solid insulation slowly deducts years off a transformer’s life.
One way to think about it is that the paper’s lifespan is cut in half every time the moisture content doubles. And every year of delay in fixing the problem chips away at approximately two years of reliable service. That valuable loss of transformer life is all due to the deteriorating condition of the paper. Therefore, we like to say, “the life of the paper is the life of the transformer.”
“The life of the paper is the life of the transformer.”
Moisture Removal Options
There are three common ways to reduce the moisture levels in a wet transformer.
Method 1 – Online Dryer (DryMax)
The first method is the most recommended field procedure to dry a transformer. This method uses an online passive dryer, like SDMyers’ DryMax technology. The online dryer connects directly to a live transformer for as long as it takes to remove moisture. Upon installation, it immediately prevents further degradation of your paper insulation to improve transformer reliability. Online dryers are popular because they do not require de-energizing the transformer or taking it offline and can be installed and re-installed throughout an entire fleet of transformers. This is the only moisture reduction option that dries the paper insulation while the transformer remains in service.
Method 2 – Field Dehydration
Field dehydration is a method that circulates the transformer liquid insulation through a mobile oil processing unit that comes onsite. This process uses heat and filtration to remove moisture from the oil as it circulates through the unit and takes approximately one to two days to complete. Field dehydration will remove moisture from the oil but will not effectively remove moisture from the paper insulation.
Method 3 – Field Dry-Out
Field dry-out is where heat and direct vacuum are applied to the transformer tank after the unit is completely drained of fluid. The transformer must be rated for full vacuum and be leak free. This usually results in an extended outage due to processing times and set and idle times. Often multiple cycles of heat and vacuum are applied. Cold traps are used to collect and measure the drying process; the temperature will affect the efficiency of this process. Electrical testing can also be a valuable tool to determine the effectiveness of the procedure. Insulation power factors of less than 1% are desirable for most service-aged transformers.
Prioritizing Moisture Reduction
A transformer is only as strong as its weakest link, and the weakest link is its paper insulation. For this reason, transformer owners should prioritize moisture reduction services as an investment in their equipment assets. While moisture can prematurely end the reliable life of a transformer, mitigating this issue early and consistently can be straightforward and relatively inexpensive compared to the alternative risk of unplanned downtime, premature failure, and transformer replacement. Investing in and prioritizing moisture reduction is the best way to create a proactive plan to protect an entire fleet for its entire lifespan.
April 04, 2023