Substation asset life extension
Your substation is a complex hub of high-voltage equipment that works hard every day to power your production. Do you know your critical substation assets? Do you have strategies in place for maintaining them?
Click on the substation components below to learn more about what they do, why they fail, and how you can prolong their reliable life.
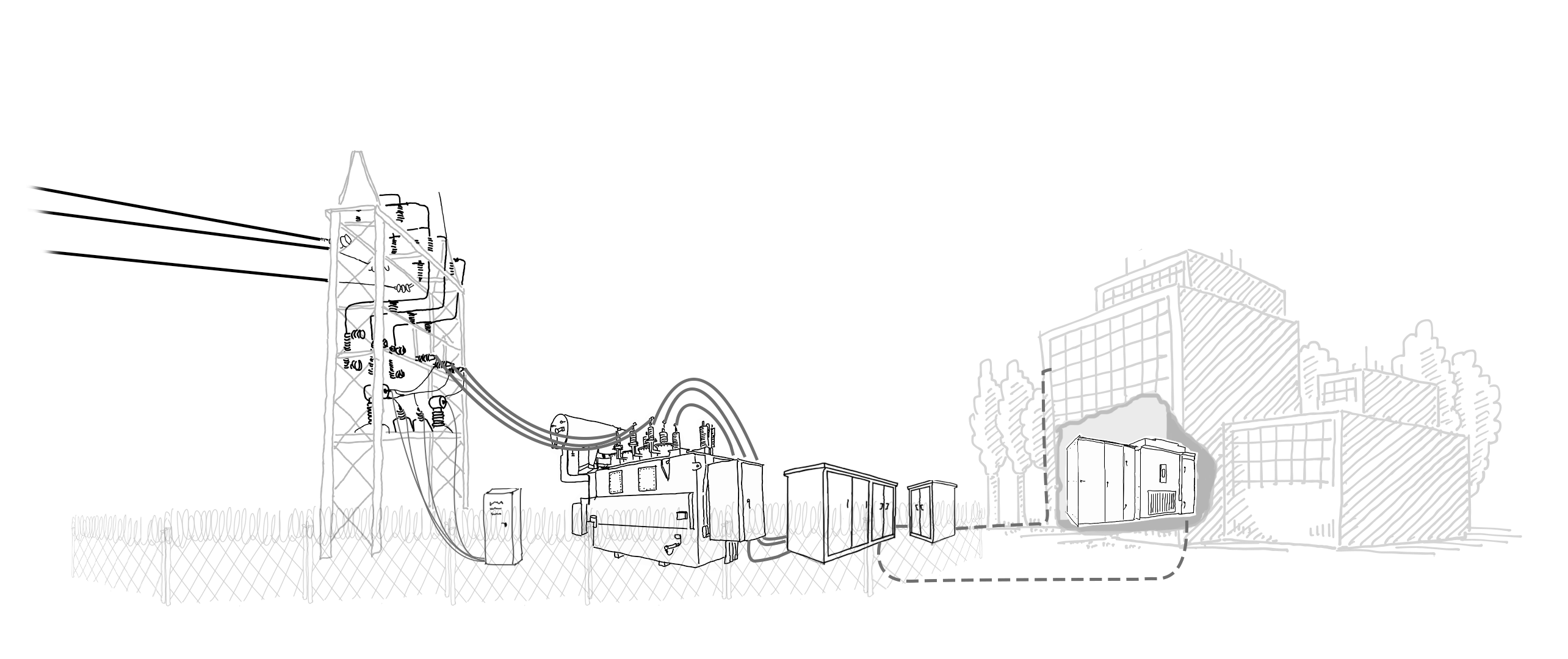
Keep learning!
Here’s a not-so-fun fact. Industrial transformers have a life expectancy of 20–25 years, but more than 70 percent of U.S. transformers are already on borrowed time. Other substation components are only made to last a decade. Getting the longest reliable life from your substation assets is a complex endeavor. Feel free to browse our blog to continue your quest for substation knowledge.